Audit Program Results
2007 Results
In 2007, 14,264 audits in 8,246 supplier factories were conducted by Wal-Mart's ethical standards group and third-party audit firms. Of the audited factories, 6,141 produced merchandise for direct imports and 2,105 produced domestically-sourced merchandise. We also accepted 1,306 audits conducted by the International Council of Toy Industries (ICTI) and the International Labour Organization (ILO). The ICTI and the ILO audits are conducted under a shared standard and are accepted by multiple brands and retailers.
We conducted fewer audits in 2007 than in previous years due to changes in our program regarding audit frequency. The 2007 re-audit timing for yellow-rated factories was lengthened from 120 to 180 days. This change allowed factories ample time to remediate any issues, as well as to provide an improvement incentive to lower-rated factories. This extended audit period led to a decrease in the number of follow-up audits that can occur in any given year. Additionally, our regional managers in Europe and South America have indicated that suppliers attempting to source merchandise in these regions have experienced a decrease in the number of available facilities due to factory closures. We believe this reduction caused suppliers to align themselves more closely with the best-performing and most stable factories, which are audited less frequently. As a result of these changes and other factors, the overall number of audits declined by 15 percent compared to 2006.
2008 Results
In 2008, our audit volume declined by 19 percent compared to 2007. Wal-Mart's ethical standards group and third-party audit firms conducted 11,502 audits in more than 7,000 supplier factories. Of the audited factories, approximately 5,000 produced merchandise for our direct import program, and 2,000 produced domestically-sourced merchandise. In 2008, we accepted more than 1,000 audits from the ICTI and ILO. We attribute the decline in overall audits in part to the change in the program's frequency of audits. Additionally, the factory base across many regions has been negatively impacted by the unfavorable global economic conditions, thus leading to factory closures.
In addition to auditing, we launched our prequalification program to evaluate a factory's compliance with our ethical standards before production of any merchandise for Wal-Mart.
In evaluating our 2008 results, we recognized improvement in green ratings in four regions and stable or improved yellow ratings in three regions. The most promising changes occurred in Africa, the Middle East, Northern Asia, India and Europe. We attribute these improvements to suppliers who discontinued sourcing from poorly performing factories and the implementation of programs designed to facilitate learning and cooperation. An example of this improvement can be found in the European region, where the audit result improvements are the outcome of time and effort expended into educating and supporting our suppliers in performance improvement initiatives. We were able to move suppliers from yellow to green by working with them in areas such as health and safety management.
GSCP Progress Update
As part of the Global Social Compliance Program (GSCP), we supported establishing a common set of global standards for factory audits by participating in the creation of the GSCP "Reference Code." Launched in December 2008, this initiative allows Wal-Mart to accept the results of an audit performed by another retailer or brand, provided that the audit was completed using the standards set out in the Reference Code. As the code used to perform the audits is agreed upon and recognized by multiple brands and retailers, one audit performed at a factory can satisfy the compliance needs of that entire group of companies, and is therefore shared among them. Sharing audit results eliminates the need for each of the companies to conduct its own audit with its own individual standards. As a result, the audit process becomes more efficient, causes less disruption in the factory, and lowers operating costs for the factory. We have piloted the use of these common standards, and we are currently participating in the auditor certification and equivalency program.
Regional Challenges
Each operating region within the Ethical Standards program faces specific challenges stemming from conditions as varied as the regions themselves. We strive to understand the root causes that bring about these challenges.
Asia
Southeast Asia
In Southeast Asia, we often encounter factories that do not comply with work hours standards, specifically standards that focus on workers not exceeding the work hours as defined by regulations or by contract. Additionally, due to the relative mobility of laborers in this region, supplier factories producing merchandise for sale at Wal-Mart also frequently experience language barrier issues.
Far East
In the Far East region, we commonly encounter factories that do not comply with the work hours standards, specifically the standards related to the permissible maximum number of regular work hours and overtime hours that a worker is allowed to work during a given day, week and/or month. Additionally, inconsistent time records are often found in this region, and we also have noted that many factories in this region are not paying all mandated benefits to workers. Lastly, the Far East region, in late 2008, experienced a labor surplus because of the downturn in the economy.
Africa, Middle East, Indian Subcontinent
The disparity of government-mandated minimum wages between local and migrant workers is a significant challenge in this area. Additionally, this region is dealing with the re-emergence of the manufacturing industry after numerous factories had closed in 2007 and early 2008 due to a lack of business, and now certain countries within the region are experiencing an increase in order volume which is causing difficulty for factories to maintain appropriate staffing levels. Lack of staff can lead to excessive working hours for employees in order to complete product orders and the use of unauthorized subcontracting.
Europe
European Region
This region experiences violations on three different levels — low, medium and high. Low-risk violations are mostly found in Central and Northern Europe and frequently consist of inconsistent time systems, and poor health and safety management among small suppliers and/or factories. Medium-risk violations, mostly occurring in Eastern Europe, consist of wage underpayment, fire safety violations and poor housekeeping in facilities. High-risk violations found in this region include excessive working hours, poor working conditions and discrimination.
The Americas
Central and South America
In the Americas region common challenges for factories revolve around working hours and pay, such as excessive working, proper compensation for overtime and paychecks being incorrectly calculated.
Audit Ratings by Region
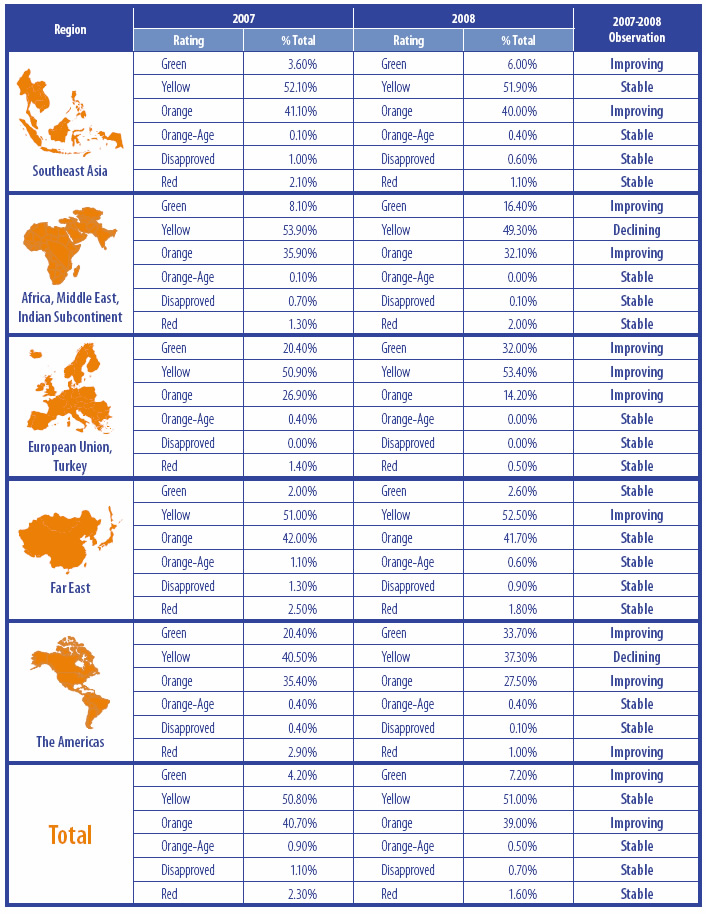
A New Direction
To date, our ethical standards program has primarily focused on evaluating and recording factory performance through our auditing process while assisting individual suppliers with remediation and conducting training programs on a regional level. Our program did not, however, allow us to effectively assist our supplier partners with implementing improvements on the floor of their factories or help our supplier partners resolve audit findings.
From an internal company perspective, the work we have performed to date gives us a strong foundation in auditing, but we recognize the existence of a gap between the current performance of our program and the expectations we have for our Company. Difficult issues still exist, and some of our suppliers' factories continue to struggle with issues related to labor work hours, discrimination, health and safety and the environment. Internally, we face challenges with on-time order placement and merchant education.
Moving forward, we will foster stronger and broader collaboration among our suppliers, stakeholders and partners, including the GSCP, Multi Fiber Arrangement (MFA) forum and ILO/International Finance Corporation (IFC) Better Works Program, to expand our efforts in supplier development. Additionally, our intent is to support our audit program with validation and investigation audits. In 2008, we laid the groundwork that will enable us to implement this strategy throughout all our regions, and we look forward to continued progress in 2009 and beyond.
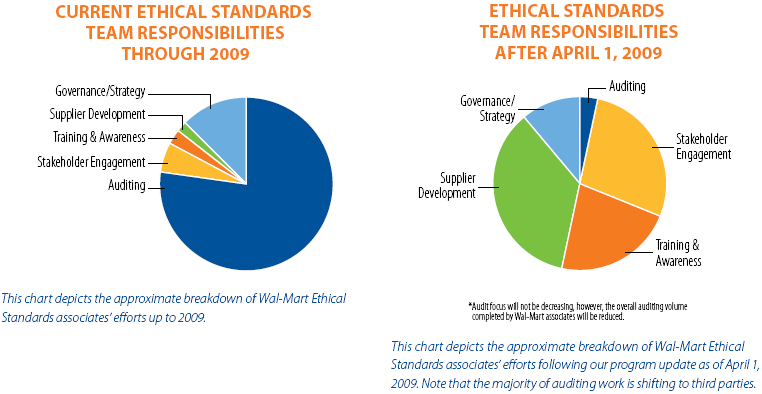
Throughout 2009, we will be transitioning the majority of our field auditing responsibility from Wal-Mart associates to third-party service providers, including Intertek NA Inc., STR-Responsible Sourcing, Accordia Global Compliance Group and Bureau Veritas. We will require that all third-party service providers complete a training and accreditation process to ensure a consistent and high-quality work product. The audit firms will be assigned to specific regions where we source merchandise; Wal-Mart-approved auditors will conduct the audits of supplier factories. To maintain rigorous program oversight, Wal-Mart will review third-party audit results and will continue to determine (assess) factory ratings.
The move to third-party auditing allows us to fulfill two goals. Our first goal is to expand our focus on supplier development. During the past two years our Ethical Standards associates have trained more than 14,000 suppliers and members of factory management, covering topics such as best practices sharing or on-site practical training. We recognize the need to further improve the ethical performance of our supplier base. In order to effectively meet this need, many of the Wal-Mart field associates who previously conducted audits are participating in extensive training and focusing their efforts on either our supplier development program or on a special audit team. Validation of the third-party audits, along with investigation audits that arise from external allegations, will continue to be conducted by Wal-Mart associates, and all such audits will be unannounced. The second goal relates to the expansion of our program's scope. By utilizing third parties, we can effectively manage the many thousands of incremental audits that our process requires be conducted each year.
This change, however, will not limit our exposure to on-the-ground issues. Our supplier development specialists will be present in the factories working on development opportunities, and we will require that our green- and yellowrated supplier factories complete self-assessments every six months. We believe these measures will keep us apprised of factory activities.
Our new strategy will include:
- Advancing our commitments
We will work with our suppliers to help them succeed under the new goals, initiatives and guidelines set during our Sustainability Summit in Beijing. - Third-party auditors
Third-party auditors will undergo thorough, independent assessments of their performance and work product quality. Third parties will be required to obtain and maintain certification to established industry standards. - Improving the efficiency of our audit program
We are a member of the Fair Factories Clearinghouse (FFC), that enables us to share data among a group of global brands and retailers. We also have developed a plan to accept high-quality and fully verified audits from peer companies, and have created a program to evaluate and accept the audits conducted by third-party groups. - New requirements
We are improving supply chain transparency by requiring all manufacturers of direct import, non-branded and private-label goods to disclose their factories and subcontractor factories. - A supplier development team
This team will specialize in supporting our suppliers and their factories through activities such as rootcause analysis. - A special audit team
Members of this team will be responsible for validating audit results generated by third-party audit firms and conducting investigation audits when ethical standards issues arise. - Unannounced audits
All audits conducted after the initial audit will be unannounced. - Internal Wal-Mart education and awareness
We will communicate how our associates' work activities can positively or negatively impact responsible sourcing. We will also partner with Wal-Mart merchant training groups to develop curriculum on responsible purchasing practices.
Supplier Development Program
Through our supplier development program, we are employing collaborative techniques to help our suppliers develop the skills they need to monitor and manage the factories they use. This program is designed to give our supplier partners both an understanding of how responsible sourcing issues are identified and the capacity to proactively resolve those issues in their factories.
The three-phased approach to our supplier development program enables us to work with select suppliers chosen by Wal-Mart's sourcing and merchant organizations through continued progression and achievement. The first phase of the program focuses on securing the supplier management's commitment to work with their factories to achieve certain social and environmental goals. The first phase also includes an initial assessment of the supplier's social and environmental management system. During the second phase, we will verify the effectiveness of the supplier's management system and provide suggestions on ways to improve the social and environmental performance of factories. In the final stage of the program, our focus is to help our suppliers improve their ability to independently address and resolve social and environmental challenges. The chart below provides a more detailed look at the program.
This program will help us meet our goal of having all of our direct suppliers by 2012 sourcing 95 percent of their production from factories receiving Wal-Mart's highest ethical standards ratings. Development challenges may occur in suppliers' factories, causing them to drop to a rating below yellow. We are committed to working with our suppliers that temporarily fall below our highest ratings and, using the supplier development program, will help them resolve issues and achieve a better rating.
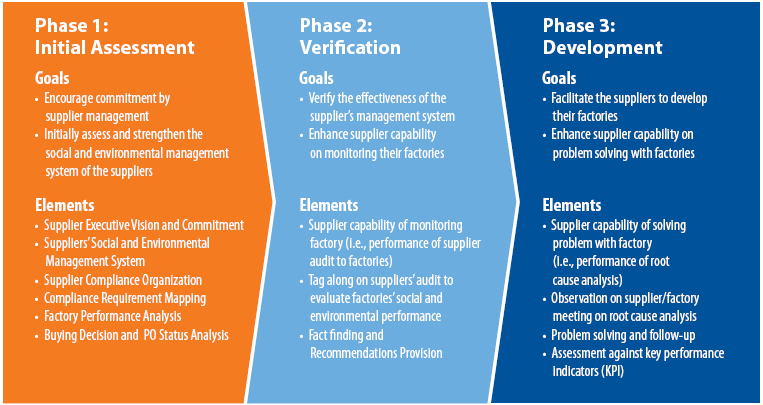