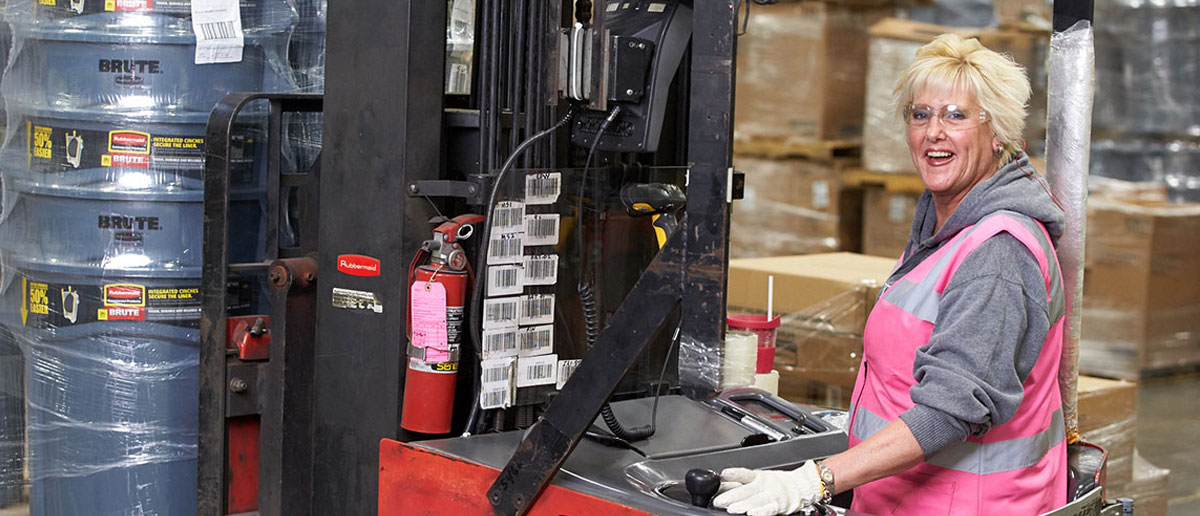
Supply Chain
Social Compliance Programs
Newell Brands considers our suppliers to be extensions of our business and, accordingly, expects them to conduct their businesses ethically and in a socially and environmentally responsible manner. In 2017, we updated our social compliance program and harmonized it across all Newell Brands. This included updates to key program materials such as our Vendor Code of Conduct and Responsible Sourcing Manual to outline compliance standards and expectations for suppliers. The program has been recognized as a leader by customers such as Walmart, Costco and CVS.
Social compliance audits are one way we learn of supplier risks. We use audits as a starting point to drive long-term sustainable improvements with our suppliers. Audits are conducted against our Vendor Code of Conduct and assess suppliers on laws and regulations, wages and benefits, working hours, labor practices, environmental health and safety and subcontracting. Based upon findings from audits, we develop comprehensive corrective action plans with suppliers that apply root cause analysis with a focus on full issue resolution and continuous improvement.
social compliance audits
conducted 2017
We use audits as a starting point to drive long-term sustainable improvements with our suppliers.
Continuous Improvement
We help our suppliers improve through both in-person and online training. In late 2017, we brought together 400 representatives from strategic suppliers across divisions for training events in Shenzhen and Shanghai, China. At these events, we invited suppliers to share how they have been able to drive performance within their own factories and turn challenges into successes. The events culminated with an award ceremony recognizing outstanding suppliers. Training topics included:
- Social compliance program and overview
- Audit trends, top findings and remediation strategies
- Compliance software overview
- Establishing effective management systems and best practices
- Supplier presentations: examples of factory continuous improvement
- Walmart responsible sourcing presentation and program updates
- Working hours and continuous improvement
- The importance of transparency
- Building a proactive culture of fire safety
- Environmental protection campaign
- Subcontractor management and requirements
- Supply chain security
Newell also conducts quarterly webinars on topics including corrective action plans, environmental management systems, engagement of factory supervisors and recognizing and preventing forced labor. Divisional trainings with internal teams continue with the goal of driving program awareness and engagement from internal stakeholders.