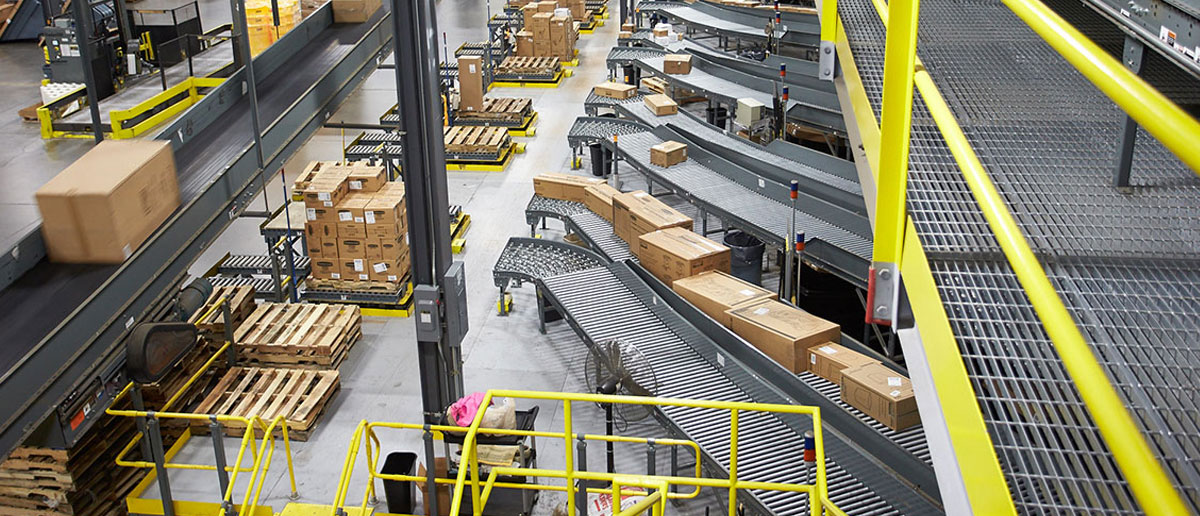
Operations
Goals & Progress
Newell Brands practices good corporate citizenship by working to decrease our operational footprint. Since our April 2016 acquisition of Jarden Corporation, Newell Brands has developed new goals for reducing our impact relative to our 2016 baseline:
- Reduce overall energy use by 25 percent by 2025; and
- Reduce waste to landfill at top manufacturing sites by 90 percent by 2025.
As of the end of 2017, we have reduced energy use by 4 percent and waste to landfill by 20 percent versus 2016. Newell Brands has created discipline in our progress toward these goals through science‑based targets, which we initially established in 2015 and are updating to reflect our broader portfolio. We also use a real‑time analytics platform for our major facilities that utilizes smart meters and a cloud computing application. With this platform, our manufacturing facilities can visualize energy usage with pinpoint accuracy and receive information critical to improving the efficiency of their equipment.
Our customers are also inspiring us to do more. Building upon Walmart’s Project Gigaton, Newell Brands is partnering with Walmart to reduce CO2 emissions by 150,000 metric tons by 2025 across our supply chain. We will accomplish this through changes in transportation, logistics, manufacturing and packaging.
Sustainability Governance
Oversight for sustainability at Newell Brands rests with our Sustainability Council, which is comprised of a cross‑functional mix of senior‑level employees that help to shape the strategic direction for our sustainability program. This council continues to evolve and expand to reflect our new organization.
The council is supported by Sustainability Champions, employees across Newell who lead the charge to improve environmental performance, operational efficiencies and cost savings at their respective locations. These Champions participate in quarterly calls with our Sustainability Council to share initiatives and successes. In 2017, we introduced a new web-based portal for easy access and collaboration. Champions use this platform to share their local success stories, but also to share ideas and engage across the Champions network. In 2017, we had nearly 70 Sustainability Champions and 150 initiatives posted on the web portal. The Deployment Committee continues to onboard new Champions with the goal of having representatives from each of our locations to further drive performance.
Success Stories
A Cutting‑Edge Solution for Producing Blades
Our manufacturing facility in McMinnville, Tennessee produces professional beauty, barber and animal grooming tools under the Oster Professional Products brand. At the heart of the business are the blades that are produced for the finished clippers. A byproduct of blade production is a coolant and water mixture that cannot be ultra-filtered and must be disposed offsite. Five years ago, the facility was generating about 5,000 gallons of this waste coolant water at a disposal cost of roughly $1,750 per week. Since then, the site has invested in a gas-powered evaporation system that boils the water off of waste liquids, leaving only the sludgy solids for disposal. The installation has prevented 750,000 gallons of wastewater from being shipped to the landfill, reducing disposal costs by more than $237,000 over that period.
gallons of wastewater
Shining Light on Energy Savings
When a local utility company near Sedalia, Missouri offered a rebate for LED lighting upgrades, our Jostens facility decided to take the plunge. We replaced 72 high bay lights with 31,000-lumen, 225-watt LEDs. The rebates covered the cost of the lights, so all the facility had to pay for were taxes. The facility will also save over the long run: the new lights draw 37 percent less energy than their predecessors, leading to annual savings of $10,000.
energy savings
Making Corrections for Efficiency
Our Liquid Paper facility in Thailand is implementing improvements and boosting employee knowledge in all areas of environmental management. The facility has a goal of reducing electricity consumption by 15 percent and annual water use by 3 percent. Energy reduction projects include updating large equipment, such as chillers, that significantly affect the facility’s energy usage, saving approximately 1 million watts of energy for certain processes. The facility is also currently evaluating the installation of solar panels. In addition, the facility sells all solvents and waste to recyclers and waste management companies.
-15%
electricity consumption